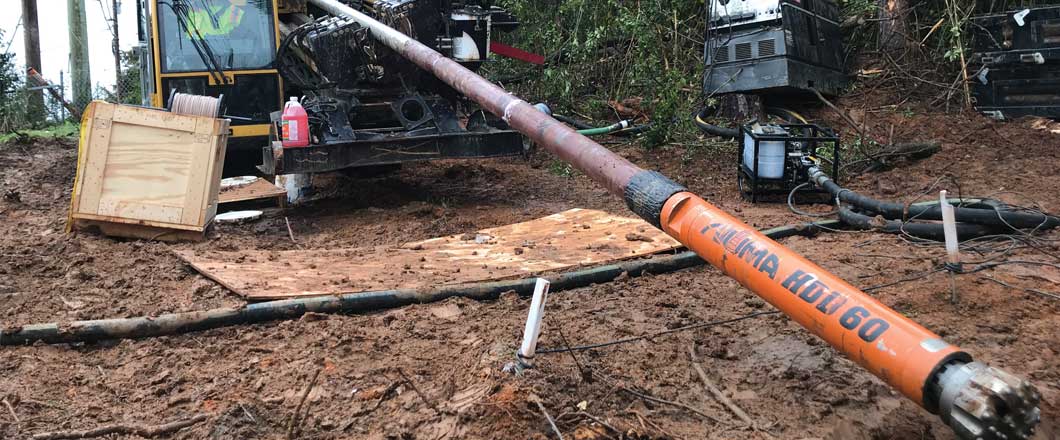
6 tips for tackling hard rock hdd projects
There has been robust demand for horizontal directional drilling (HDD) over the last several years and the trend is forecast to increase through the next decade. Driven by growing communication and energy needs, HDD drilling contractors are faced with more and more challenging environments for laying underground cables, pipes and conduits. Now, more than ever, contractors need the right tools to complete projects in the most efficient and safe manner possible.
Conventional HDD tools like blades or jetting assemblies are well suited for many applications. However, these products do not provide the most effective methods when encountering rock formations. When a contractor gets into rock, traditional tools can slow a project down and increase cost significantly. The good news is HDD rock drilling tools are available to help get job done quickly and efficiently.
There are six key considerations every HDD contractor encountering rock must make in order to have a successful project.
1. Use HDD Air Hammers for Rock
Many of the leading HDD contractors have adopted the use of air hammers for drilling in rock formations. Air hammers have a big advantage over conventional HDD tools used for drilling in soil. Foremost is the ability of air drilling tools to drill in many different formations including hard rock, fractured rock, gravel, boulders and unconsolidated materials. Air tools also offer an optimum rate of penetration when faced with these conditions. Plain and simple, air drilling tools are much more efficient when dealing with rock and can cut drilling time in half or even more.
2. Have All Tooling Available Onsite
Formations and/or project designs can change so you need to be prepared to handle many different requirements in the field. As mentioned, HDD drilling tools are specific to the formation being drilled. Contractors need to have the right tools in their toolbox. Dirt drilling requires a blade or jetting assembly which is seen in many applications. In rock formations, air hammers are required. Drillers should also have a swivel to match the pull rating of the drill rig for installation of final product. Hydraulic safety tongs are also recommended for safely torquing and breaking connections. It is also recommended that drillers keep spare consumables such as starter rods, hex collars, bits, sonde housing, etc. Drillers need to be prepared vs. scrambling to meet the needs of the job.
3. Maintain Tools to Promote Long Life
It is a simple thing but proper maintenance is overlooked by many contractors. It is easy to just put tools back on the truck and forget about them until the next project. This practice costs drillers money. Cleaning all tooling after each project is the best method to protect an investment in HDD tooling. Drillers should pay particular attention to making sure to grease swivels after use. For air hammers, be sure to blow the hammer clear after use, pour 1 quart (1 liter) of rock drill oil into the backhead, and cycle for 10 seconds. Then store the hammer in a horizontal position in a dry environment. For long term storage, hammers should be disassembled and components inspected to ensure all parts are in working order and drill strings do not get contaminated.
4. Considerations When Buying HDD Rock Drilling Products
Not all drilling products are the same. The old adage of, “You get what you pay for” applies here. All drilling components on the jobsite from the rig to the drill bits need to work in unison in order to get the project done. Contractors can’t afford to have inferior products slowing down to job. Drillers should focus on the following when buying HDD rock drilling tools to put themselves in the best position while in the field.
- Match the proper tooling to drill rig capabilities and formation to be drilled.
- Evaluate tooling cost vs. job pricing per foot.
- Determine if custom set-ups and tooling is required.
- Invest in tools that provide steerability, fast penetration rate, simplified field maintenance, reduced air requirements and lower overall cost per foot.
- Understand the reputation of the tooling manufacturer and the products they provide.
- Align yourself with organizations providing the right expertise, training, and support before, during and after the project. Hint: A reputable manufacturer should do this.
5. Common Mistakes
There are times that “stuff” can happen but doing the proper homework and establishing a plan of action goes a long way for a successful project. The best HDD drillers will always do the following to avoid common mistakes:
- Gather accurate geotechnical information. It is critical to know the formations and type of applications the project will encounter before starting up.
- Select the right tools for the job. Using tools thought to be “good enough” can lead to projects taking longer and costing more.
- Properly size tooling to the product being installed. Do not over or under-size the tools required to do the job right. Ensure the final hole size is 1.5 times the outside diameter of the product being installed.
- Acquire expertise and training if you are not accustomed to using HDD rock drilling tools.
6. Lubrication & Contamination
HDD air hammers rely on a supply of clean lubricated air to operate properly. The hammer piston is a close tolerance fit with the case bore and it cycles at very high blows per minute. Failure to ensure that a clean, lubricated air supply is being provided may result in overheating, material pick-up, seizure, or failure. Also be mindful hose ends may be accidentally contaminated prior to connection and drill strings may be contaminated during storage. Even new hoses and drill string parts can be contaminated from the factory. Be sure to follow manufacturer’s recommendations for proper lubrication and contamination prevention when operating air hammers.
With underground fiber, telecommunication and other utility projects forecast to increase into the foreseeable future, the drillers who develop expertise and adopt new drilling practices will be the ones who get ahead. Following the insights above will help forward-looking organizations do just that and successfully deliver on HDD rock drilling projects.