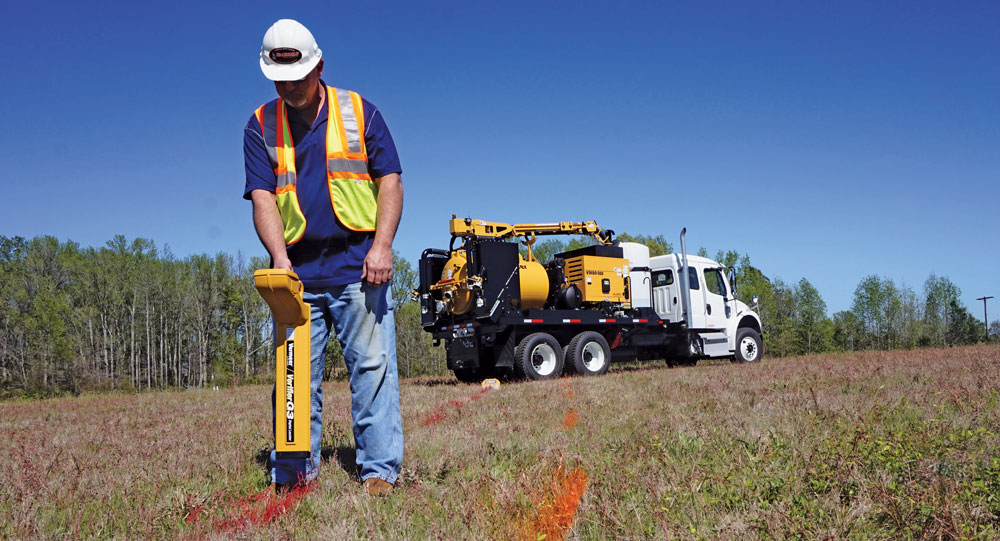
HDD- The Importance Of Inspection
The drilling unit along with the drill-rods/pipe are the pieces of equipment that take the strain of every job and without them the HDD rig operation comes to a standstill. But everyone is aware of the implications of Non-Productive Time (NPT) caused by drill stings parting or damaged drill pipe on rigs and the costs that can be caused by neglecting the very equipment that is primary to any drilling project. So, it is essential to consider the potential cost of ‘Lost-in-Hole’ equipment.
How can operators prevent this cost, how can they mitigate the risk of drill strings parting, can operators ensure clients that they have maintained the equipment regularly and consistently and place liability away from the equipment? Has anyone thought about NDT Thread & Drill Pipe Inspection Services?
SlimDril has for over 20 years provided thread inspection certification for any of the equipment it sells, rents or repair, this ensures the equipment is ready for use and the client has the documentation to support it, but SlimDril went that bit further and in September 2021 started a Thread Inspection and Restoration Service.
The service is fully mobile and inspections can be carried out onsite, at the client premises or indeed at the SlimDril Facility. The company’s lead inspector has over 30 years of working knowledge and experience of inspection and restoring threads where possible, the inspector will show the client the damage to threads, the cracks and the wear to a wide range of drill pipe, threaded tooling and cross-overs.
The company can re-face seal areas on site, re-dress threads (both where it is possible to be able to do so) and provide advice on conditions for use. The service is to ensure the drilling contractors clients that all equipment is ready for use and offers the client an insight into the ‘Risk-Management’ of the drilling contractor in preparation for a project.
Slimdril has been asked what is the timeframe between inspections, in truth there is no hard and fast rule and it is up to the drilling contractor but it does make lots of sense financially and progressively to ensure regular intervals between inspections. The cost of the inspections can also be passed to client’s projects as equipment that is damaged on a project can be back charged because it was indeed damaged on that particular project, as a pre-job inspection certification would prove. So, advancing risk management, controlling downtime and maintaining the spine of operational tooling are vital ingredients in a successful project.
What else does an inspection look for? Several things including:
• Crack indications in threads
• Crack indication in box connections
• Crack indication in outside upsets• Galled threads
• Pulled threads
• Over-torqued threads
• Galled seals
• Seal damage to shoulders • Pitting/corrosion
• Washout in connection Prevent that NPT!
As stated previously, thorough inspection is vital. The pipes need to be able to take the load capacity, the thread dimensions must be correct and fatigue needs to be eliminated. Failure to do so could result in the drill string coming apart and anything that is left would need to be fished out of the hole or (if you are unlucky) be left in the hole. All this results in a lot of NPT with very expensive consequences. Something no-one wants!